Most z fabryki – komu, komu?
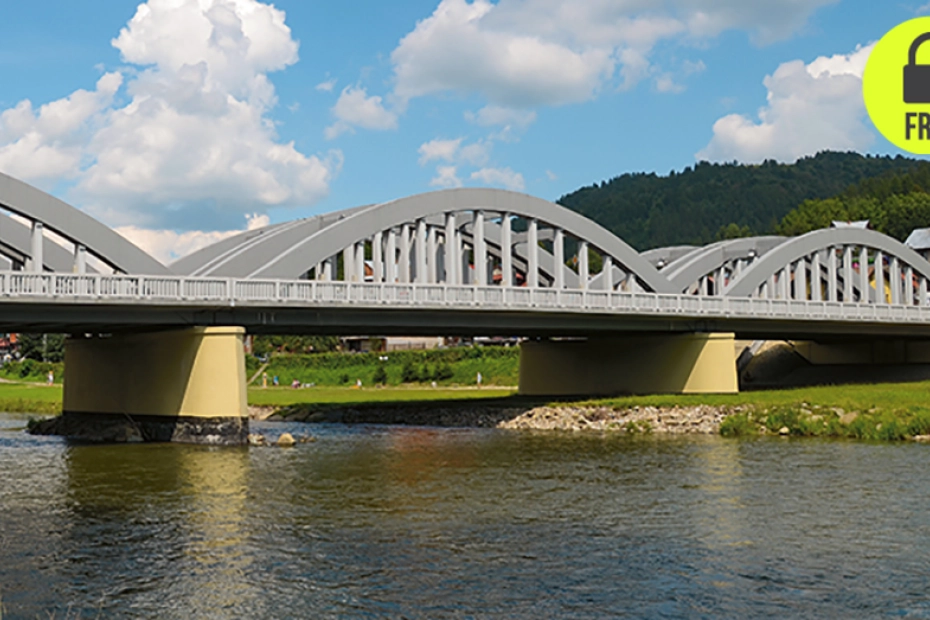
z miesięcznika „My Company Polska”, wydanie 1/2015 (1)
Zyskaj dostęp do bazy artykułów z „My Company Polska” Zamów teraz!
Mosty to symbol cywilizacji, ale także jej newralgiczny punkt. Wyobraźmy sobie miasta nad rzekami, które zostałyby ich pozbawione. Dlatego, zdaniem prof. Janusza Rymszy, zastępcy dyrektora Instytutu Badawczego Dróg i Mostów w Warszawie (IBDiM), mosty mają być, przede wszystkim, funkcjonalne. Powinny służyć codziennemu życiu milionów ludzi, a nieliczne mogłyby też zachwycać swą wyjątkowością. – Niech będzie nawet 5 proc. oryginalnych mostów, lecz pozostałe powinny być typowe, to znaczy łatwe do zaprojektowania, szybko stawiane, bardziej trwałe od tych niezwykłych, sprawnie naprawiane, a kiedy trzeba – mądrze rozbierane – wylicza profesor. Dzięki temu, będą tańsze w budowie i eksploatacji.
Pochwała prostoty
Niezwykłe mosty robią wrażenie, lecz stanowią ogromne wyzwanie dla administracji. Koszty ich utrzymania są kilka razy większe niż w przypadku typowych obiektów. Świat jednak zachłysnął się technologicznymi cudeńkami. Jesteśmy spragnieni rzeczy autorskich, „kolorowych”. Chcemy tego, co postawione na głowie. Prostota, zwyczajność, wielu dziś rażą. Tymczasem, jak podkreśla prof. Rymsza, szansą dla światowego budownictwa mostowego są prefabrykaty: modułowe podpory, pomosty, przęsła, belkowy lub płytowy tzw. ustrój niosący. To wszystko można wyprodukować w fabryce, a na budowie złożyć w całość. Potem, w trakcie eksploatacji, łatwo da się wymienić zużyte czy zniszczone elementy. Wizytówką tej technologii są mosty zbudowane przez firmy zrzeszone w konsorcjum „Most w 3 miesiące”, utworzonym w 2008 r. pod przewodem IBDiM. Przystąpiło do niego pięciu polskich wykonawców, cztery biura projektowe i trzy ośrodki naukowe, a na badania i ich wdrożenie dostali dotacje z UE.
Rezultat? Np. most w Łodygowicach, w powiecie żywieckim. Postawiła go w zaledwie sześć tygodni spółka Mostmarpal z pobliskiego Zarzecza. Przerzucenie mostu przez wąską rzeczkę, taką jak w Łodygowicach, zajmuje zwykle kilka miesięcy. Przeprawę średniej wielkości (50-metrowe przęsła) buduje się przez rok, ale przy użyciu technologii opracowanej w konsorcjum – przeciętnie przez trzy miesiące. Pale wkręcane, na których opiera się cała konstrukcja, przyjeżdżają gotowe z fabryki. Tradycyjnie – powstają na budowie: wlewa się cement w wywiercone otwory i czeka, aż stężeje, przy czym często trzeba ten proces ponawiać. Albo montaż przęseł stalowo-żelbetowych (tzw. gzymsów). Konsorcjum opracowało technologię ich produkcji, która w fabryce pozwala zaoszczędzić na materiałach, a na budowie łączyć je szybko metodą pióro-wpust, zamiast spawać. Wszystko to zmniejsza koszty i skraca czas realizacji, zwiększając rentowność wykonawców. Ma też znaczenie dla okolicy, gdzie powstaje most. O wiele krócej odczuwa się utrudnienia w ruchu. Koszty społeczne można dzięki temu zredukować do minimum.
Dlaczego tylko 20?
Jak dotąd, w ramach konsorcjum stanęło w Polsce ponad 20 „mostów z fabryki”. To niezbyt imponujący wynik. W samym tylko powiecie nowotarskim w latach 2010–2014 przebudowano lub postawiono 16 mostów. Większość modułowych obiektów powstała do 2013 r. Konsorcjum istnieje, ale tkwi jakby w zawieszeniu. Kolejne pieniądze z Unii pewnie by pomogły w działaniach marketingowych. Bo, generalnie, potrzebna jest tu większa siła przebicia.
Obecność na targach budowlanych nie wystarcza. Potencjalnym zleceniodawcom (lecz także projektantom) należałoby np. pokazywać katalogi prezentujące kompletne rozwiązania oparte na prefabrykatach. Najlepiej, by w każdym znalazło się po kilka przykładów konstrukcji danego rodzaju, które już funkcjonują. W tej chwili jednak katalogi nie są planowane.
Są też inne przeszkody...
... związane z gorszą pozycją mniejszych budowniczych. Prof. Rymsza zwraca uwagę na zwyczaj przeciągania się dyskusji między zleceniodawcami budów, a ich wykonawcami. Ci pierwsi nie są elastyczni. Często nie godzą się na ulepszenia w projekcie proponowane w trakcie pracy przez tych drugich. Mogliby się dogadać, ale spory zazwyczaj trafiają do sądu. Mniejszy wykonawca nie jest w stanie wytrzymać finansowo procesu, który potrafi trwać ponad dwa lata.
Kolejna rzecz, to przepisy o zamówieniach publicznych. Nie precyzują niektórych kryteriów budowy mostów, jak jakość czy funkcjonalność. To dlatego zagraniczna firma, która nie ma w Polsce sprzętu ani ludzi, może u nas wygrać rywalizację o poważne zlecenie – wystarczy, że przedstawi referencje z innych rynków. A można by wprowadzić przepis, że zwycięzca przetargu musi w co najmniej 50 proc. sam wykonać projekt. Dziś wygrani biorą podwykonawców, którzy często nie dają sobie potem rady. Popadają w tarapaty finansowe, a budowa staje.
Ucieczka do przodu wspiera sprzedaż
Słaba promocja i opisane przez profesora problemy sprawiają, że kompletne mosty z prefabrykatów wciąż torują sobie drogę do serc zleceniodawców. Niemniej poszczególni członkowie konsorcjum i tak korzystają na tym, że się w nie zaangażowali. Mostmarpal twierdzi, że jest liderem na rynku głębokiego fundamentowania. Jego pale wkręcane kupują generalni wykonawcy, w tym takie koncerny jak Mota Engil. Innowacyjna technologia bardzo ułatwiła ich sprzedaż. Wspiera też strategię przedsiębiorstwa, by być w rynkowej czołówce, jeśli chodzi o nowoczesne, nietypowe rozwiązania i realizacje. Do konsorcjum przystąpiła też spółka Intop Tarnobrzeg. Całe mosty, w ramach konsorcjum, budowała do 2013 r.
Jej przedstawiciele twierdzą, że główną korzyścią, jeśli chodzi o ten projekt, było zdobycie doświadczeń w pracy z nowymi materiałami i technologiami. Wśród tych nowinek są prefabrykowane dźwigary zespolone stalowo-betonowe, czyli tzw. technologia VFT-VIB, którą po raz pierwszy zastosowano w Polsce, stawiając most w ciągu linii kolejowej Kielce–Fosowskie na Opolszczyźnie. – Takie doświadczenia liczą się podczas przetargów – podkreśla pracownik Intop Tarnobrzeg, który jednak prosi o anonimowość. Członkowie konsorcjum umówili się bowiem, że o wszystkim, co zahacza o „Most w 3 miesiące”, do mediów może się wypowiadać tylko IBDiM.
Unia przychodzi z pomocą
Zatem, wróćmy do Instytutu. Według obliczeń jego specjalistów, „życie” współczesnych mostów powinno trwać ok. 50 lat, ale ich fundamentów – co najmniej 200. Pół wieku to także okres, gdy, jeśli nie dojdzie do kataklizmu, zmienia się zwykle forma eksploatacji. Wzmacnia się most, poszerza, dostosowuje. Tym modyfikacjom sprzyja rozporządzenie Parlamentu Europejskiego z 2013 r., które wstępnie definiuje m.in. zasady przeróbki mostów. Europosłowie, wsparci opiniami ekspertów, dostrzegli ekonomiczny wymiar prostego rozwiązania: łatwe zdejmowanie pomostów w przypadku, gdy dotychczasowe przestają wystarczać – i stawianie nowych, na trwałych podporach. Tak mosty budowali starożytni Rzymianie… tak chce je stawiać konsorcjum. Może więc pora wydrukować wreszcie ten katalog.
Członkowie konsorcjum „Most w 3 miesiące”
- Ośrodki naukowe: Instytut Badawczy Dróg i Mostów (lider projektu, promuje dokonania konsorcjum wśród potencjalnych zleceniodawców i projektantów) oraz Politechnika Lubelska i Politechnika Rzeszowska
- Wykonawcy: Mostmarpal, Intop Tarnobrzeg, Intop Szczecin, MS Dobra, Mostmar (upadłość w 2012 r.)
- Biura projektowe: Promost Consulting, Europrojekt Gdańsk, Projekt Bielsko, SSF Monachium
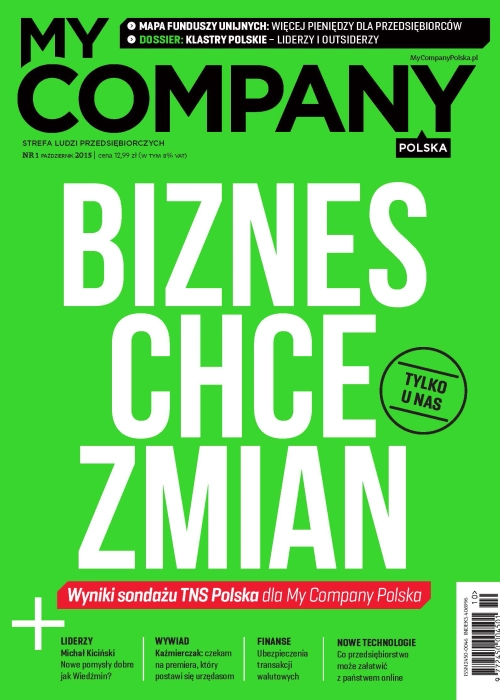
Więcej możesz przeczytać w 1/2015 (1) wydaniu miesięcznika „My Company Polska”.